Accuracy Down to the Milimeter Thanks to AR
The measurement and quality control of components is a time-consuming process. Especially in case of submarines. Holo-Light shows how augmented manufacturing can support this procedure in the future with a lighthouse project at thyssenkrupp Marine Systems.
August 4, 1906: The first German submarine slides into the water at the Krupp Germaniawerft shipyard in Kiel. For more than a year, engineers and workers feverishly built the prototype. Today, thyssenkrupp Marine Systems is manufacturing submarines and naval ships on parts of the old site – and aims to become one of the most avant-garde shipyards in Europe. This goes hand in hand with applying new technologies such as augmented reality to make production more effective, efficient and faster.
“With Augmented Reality and the Stylus XR input device, we are able to quickly detect and correct manual errors. The entire planning and assembly process is now much shorter and way more economical.”
Stefan Lengowski, Manager Development Engineering Platform, thyssenkrupp Marine Systems
From Paper to Augmented Reality
The construction of submarines is complex and accompanied by extremely high technical requirements. Several thousand components have to be aligned, welded in and inspected. Surveyors determine the position and alignment of bolts and screws using analogue 2D documents. This means that they draw the data from the CAD model on paper plans and then – equipped with the clipboard – manually mark the locations in the submarine. A time-consuming and error-prone process.
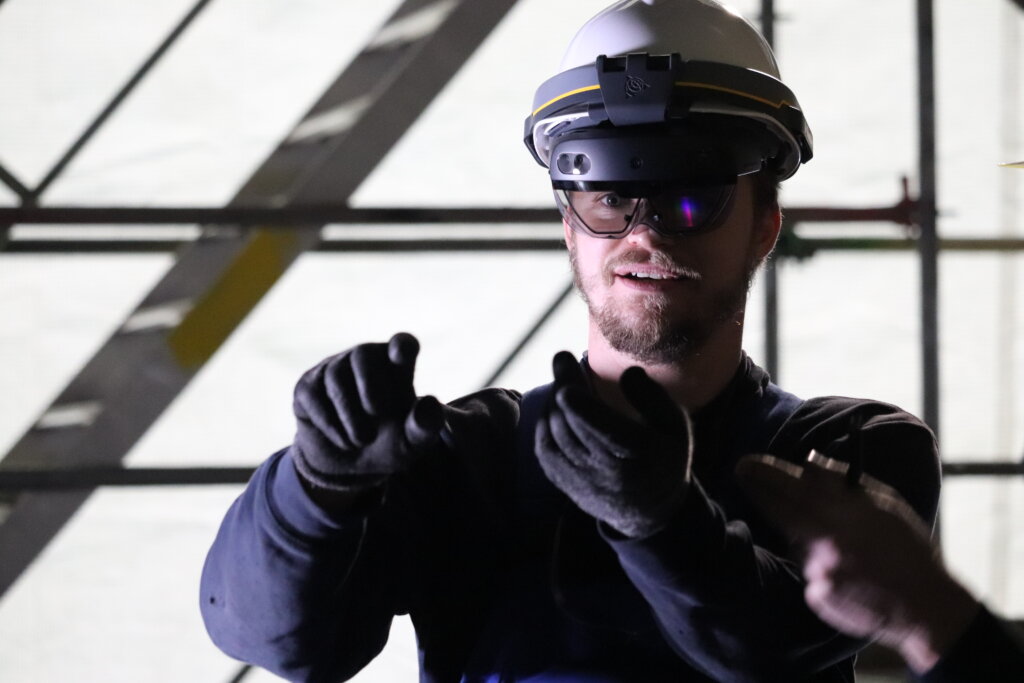
“We are always looking for innovative technologies to optimize our processes. We see augmented reality as a technology for digitizing the time-consuming measurement and quality control of components,” says Stefan Lengowski. “But we are also aware that we are facing a very challenging use case scenario.”
Comprehensive AR Solution
Holo-Light offers a unique AR solution package consisting of software and hardware. The Augmented Reality Engineering Space (AR 3S) enables engineers to visualize, manipulate and share CAD data in 3D. The software suite is complemented by Stylus XR, an AR input device with artificial-intelligence-based tracking technology. This enables engineers to perform millimeter precise work in an augmented reality environment. With an accuracy of 1-2 mm, the Stylus XR serves as a basic measurement and referencing device for submarine components.
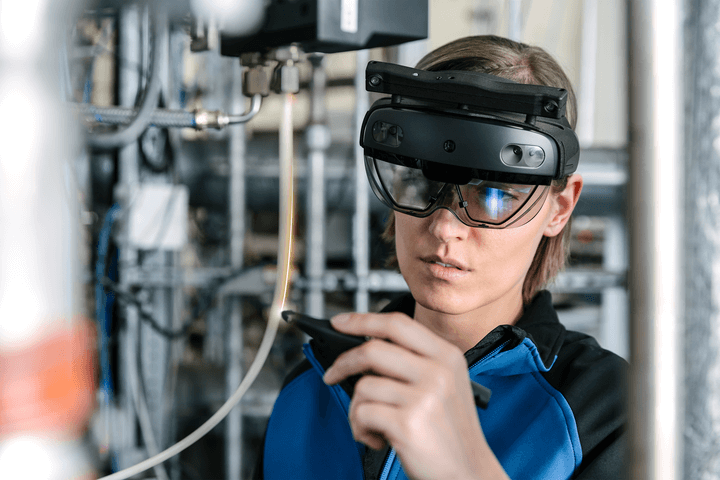
The AR expert is also relying on strong partners such as Microsoft and Trimble to implement the solution at thyssenkrupp Marine Systems. Using HoloLens 2 smart glasses, all components are displayed and superimposed in a real environment. Trimble in turn supplies the XR10, the only HoloLens 2 solution that is compatible with an industry-standard helmet and certified for use in safety-regulated environments.
Optimizing Processes and Avoiding Errors
The new work process is now significantly shorter and easier for the engineers. In the office, the engineer can load the 3D model (e.g. in jt-format) in the software, define the coordinates for referencing screws and bolts and upload them to HoloLens 2. The coordinates can then be selected with the Stylus XR input device. Virtual components provide markings and include visual feedback on the correct placement.
In the submarine itself, the engineer uses Stylus XR and AR 3S to precisely mark the locations where a screw is to be mounted by superimposing virtual 3D models and the real environment. Subsequently, the assembly takes place and the engineer can carry out a target/actual comparison in the submarine using the augmented reality glasses and software. “With Augmented Reality and the Stylus XR input device, we are able to quickly detect and correct manual errors. The entire planning and assembly process is now much shorter and way more economical,” confirms Lengowski.
Huge Potential for Planning and Construction
Especially for complex design projects such as submarines, AR improves planning and installation processes that were previously costly and error-prone. The resources required are lower, planning errors are noticed more quickly, and installation errors are hardly possible. As a result, costs and time can be massively reduced, while at the same time quality and speed are increased. Dr. Luis Alejandro Orellano, COO of thyssenkrupp Marine Systems, therefore sees augmented reality as a very important part of a digitalization strategy for the shipyards of tomorrow and is actively promoting the implementation of the technology.